Metalurgia prehispánica
Metalurgia prehispánica

La metalurgia se descubrió y desarrolló independientemente en distintos lugares del mundo y en distintas épocas. Este saber llegó hace 2.500 años a la actual Colombia, desde los Andes peruanos donde se descubrió hace cuatro milenios. Por su dureza o por su brillo y color, los metales tomaron un lugar importante en todas las sociedades que los trabajaron y sin duda han contribuido a forjar nuestra propia sociedad.
¿Qué es un metal?
Por lo general se define a los metales como elementos sólidos que comparten ciertas propiedades físicas, químicas y mecánicas que los distinguen. Además del brillo, la maleabilidad, ductilidad, dureza, tenacidad y elasticidad, son buenos conductores de calor y electricidad y tienen una elevada capacidad de reflexión de la luz.
Estas características se deben a que poseen una estructura interna cristalina con átomos dispuestos y enlazados de manera ordenada y específica, distribuidos en planos que permiten el deslizamiento de los átomos cuando se produce algún tipo de fuerza sobre ellos. La posibilidad de deslizamiento es la que permite la maleabilidad. Adicionalmente, su conductividad eléctrica se debe también a su estructura atómica: tienen un núcleo con carga positiva y electrones con carga negativa en movimiento alrededor, lo que permite la transmisión de calor y electricidad.
Sus características físico-mecánicas más importantes son:
- Maleabilidad o capacidad de poder estirarse en todas las direcciones sin romperse al ser sometidos a trabajos de laminación o de martillado. El más maleable de todos los metales es el oro y siguen en orden decreciente la plata, el aluminio, el cobre, el estaño, el platino, el plomo, el zinc, el hierro y el níquel.
- Ductilidad. Es una característica estrechamente relacionada con la maleabilidad y se entiende como la capacidad de dejarse deformar para convertirse en hilos. El orden de ductilidad de mayor a menor es: oro, plata, platino, hierro, níquel, cobre, aluminio, zinc, estaño, plomo.
- Elasticidad o capacidad de los metales de recuperar su forma inicial luego de una deformación momentánea producida por la acción de una carga.
- Dureza es la resistencia que oponen los metales a ser rayados. La presencia de impurezas (pequeñas cantidades de otros elementos) altera la dureza del metal.
Los metales están constituidos por cristales conocidos como granos. Cuando una sustancia pasa del estado líquido al sólido se produce un proceso llamado cristalización. Los átomos se organizan para formar pequeños sólidos geométricos como cubos, octaedros, etc., que se denominan cristales y que crecen de acuerdo al enfriamiento y hasta donde se lo permite el grano o cristal contiguo; al encontrarse forman la “frontera de grano”. Durante el enfriamiento, dentro de los cristales se crean estructuras en forma de árbol llamadas dendritas que se desarrollan en diferentes direcciones en cada cristal. Si el enfriamiento se produce lentamente, las ramas secundarias de las dendritas quedan más espaciadas y el metal es más quebradizo; si el enfriamiento es rápido, las ramas se juntan, se ven más gruesas y el metal se torna más duro.
Existen tres tipos de estructura cristalina u organización de los átomos dentro de los cristales. El oro, la plata, cobre, plomo, aluminio y níquel se encuentran empaquetados de forma “cúbica centrada en las caras”(FCC, por su sigla en inglés), y por esto comparten las mismas propiedades y se dejan trabajar de formas similares.
Los orfebres prehispánicos que habitaron el territorio colombiano trabajaron especialmente el oro, el cobre y en menor proporción, la plata y el platino. En su forma nativa el oro, la plata y el cobre contienen generalmente como impurezas cantidades variables de los otros dos; el cobre puede presentarse libre de oro, mientras que el oro nativo generalmente contiene cantidades considerables de cobre.
Oro, cobre, plata y platino
El oro
El oro es un elemento químico de símbolo Au y de color amarillo. Tanto el nombre “oro” como su símbolo se derivan del latín aurum que se refiere al resplandor, a la luz, a dorar, dorado, áureo. La palabra “orfebre”, del francés antiguo, se deriva a su vez del latín auri faber “metalúrgico del oro”, el que fabrica oro. En la antigüedad, la principal preocupación de los alquimistas era producir oro a partir de otras sustancias como el plomo.
El oro ocurre en la naturaleza como parte integrante de las rocas. Se cree que se forma de gases y líquidos que se elevan desde el interior de la tierra, los cuales viajan a la superficie a través de fallas de la corteza terrestre. Es encontrado en vetas, depósitos, en depósitos de cobre porfírico, placeres y en menor escala en el agua del mar. Las vetas están incrustadas en las rocas, mientras que los depósitos de placeres están constituidos por partículas llamadas pepitas (independientemente de su tamaño). Estas pepitas fueron arrancadas, lavadas y cargadas desde las vetas por aguas superficiales como los ríos. Raramente encontrado en su forma pura, el oro está usualmente combinado con plata en una aleación natural llamada electrum u oro argentífero.
El oro es el metal más maleable y dúctil de todos, de ahí que se puedan obtener láminas extremadamente delgadas. También es el segundo más pesado, con una densidad de 15.6 – 18.3 g/cm3; es blando (2,5 – 3 en la escala de Moh) y tiene un punto de fusión de 1.063°C. Es excelente conductor de calor y electricidad y, especialmente, es incorruptible, no reacciona con ácidos ni con el oxigeno, es decir no se oxida ni pierde su brillo; sólo reacciona con el agua regia.
El cobre
Del latín cuprum procedente del griego Kýpros, nombre propio de la isla de Chipre, donde se obtenía este metal en abundancia. Su símbolo químico es Cu.
El cobre es conocido desde tiempos remotos y probablemente fue el primer metal utilizado para fabricar útiles. En la naturaleza existen diferentes tipos de yacimientos con diversas presentaciones dependiendo de los procesos geológicos que le dieron lugar que a la vez inciden en su manera de explotación. Unos producen cobre nativo, pero otros, por la acción de los agentes atmosféricos a través de millones de años, son depósitos de cobre oxidado: la cuprita o cobre rojo, que tiene un 90% de contenido de cobre, asociada con frecuencia al cobre nativo, y los carbonatos como malaquita y azurita.
El cobre tiene un color rojo pardo característico, es pesado con un peso específico de 8.92 g/cm3 y es excelente conductor de calor y electricidad. Funde a 1.083°C y no se quema al aire pero gradualmente se convierte en óxido cuproso o cúprico cuando se calienta al rojo vivo. Aunque no suele afectarse por el aire a temperatura ordinaria, su exposición al aire húmedo sí ocasiona un revestimiento o pátina verde, característica de los carbonatos. Es un metal maleable y dúctil y presenta un alto grado de acritud, es decir, se vuelve quebradizo al ser sometido al martillado, debido a su rápido endurecimiento.
La plata
Los alquimistas de la antigüedad la llamaban el metal Luna o Diana, por la diosa de la luna, y le atribuyeron el símbolo de la luna creciente. Su símbolo químico, Ag, se deriva de latín Argentum que significa blanquecino. En el siglo IV d.C. Hispania era el principal proveedor de este metal para el imperio romano. Para exportarla se preparaba en láminas llamadas “Plattum (láminas) argentum”. Posteriormente la pérdida del sustantivo dejó sólo a platta, y así llegó a nuestros días.
La plata es un elemento bastante escaso que se forma en rocas ígneas y metamórficas en filones hidrotermales. La mayoría de las veces se encuentra como minerales que contienen compuestos de plata. Aproximadamente tres cuartas partes de la plata producida hoy en día son un subproducto de la extracción de otros minerales especialmente del cobre, el zinc y el plomo. Su aleación natural con oro se conoce como electrum.
Los yacimientos más notables de plata pura se encuentran en México y en Perú.
Después del oro, la plata es el metal más maleable y dúctil. Es el de más alta conductividad térmica y eléctrica. Es moderadamente suave y un poco más duro que el oro. Funde a 963°C. Es lustroso, de color blanco grisáceo, y cuando se pule su brillo refleja el 95% de la luz. No se oxida fácilmente pero su superficie ennegrece a causa de pequeñas impurezas de sulfuros.
Por lo común la plata se recupera de los minerales de plata por tostación del mineral en un horno para convertir los sulfuros en sulfatos y posteriormente poder extraer químicamente la plata metálica. El proceso más común es el del amalgamado, en el cual se vierte mercurio líquido sobre el mineral triturado; el mercurio forma una amalgama con la plata, que se lava y procesa para que el mercurio se volatilice y quede libre la plata.
Otra forma de beneficiar la plata es por medio de la copelación, que consiste en mezclar el metal precioso impuro con plomo: los metales se funden conjuntamente en un crisol poroso o copela (copa pequeña) hecho a menudo con cenizas de hueso. Al soplar sobre la masa fundida, el plomo y los restantes metales viles se oxidan y el óxido de plomo es en parte eliminado por el soplo y en parte absorbido por las paredes del crisol. En el crisol queda un botón de plata refinado.
El platino
El platino fue descubierto por primera vez, como metal, en Colombia; en el año de 1748 el oficial de marina español don Antonio de Ulloa y García de la Torre lo presentó en Europa. Los indígenas americanos, sin embargo, lo conocían ya dos milenios antes y lo podían trabajar por sinterización.
Su nombre proviene de la palabra española platina o plata menor, ya que inicialmente se le creía una variante de la plata. Los españoles descubrieron depósitos aluviales de este metal cuando exploraban minas en busca de oro en la región del Chocó, en la mina de Santa Lucía cerca de la población de Tadó. Allí notaron la existencia de un metal de color blanco grisáceo, imposible de fundir y con ningún uso aparente: inicialmente lo botaban de nuevo en los ríos para que, según la alquimia, terminara de madurar. Aún cuando algunos ejemplos llegaron a Europa, se experimentó gran dificultad para obtener una masa de platino maleable debido a su altísimo punto de fusión de 1.773°C.
No es un metal muy abundante en la corteza terrestre. Por lo general se encuentra en estado metálico en forma de pepitas aleado con otros metales del grupo del platino y asociado a minerales de níquel, oro, cobre y cromo.
Los placeres más abundantes se encuentran en la región del Pacífico de Colombia y Ecuador y Colombia es uno de los mayores productores del mundo.
Se trata de un metal de color blanco grisáceo, blando, dúctil, maleable, pero con un altísimo punto de fusión, lo que lo cataloga como un metal difícil de trabajar. Se expande ligeramente con el calor y tiene una resistencia eléctrica alta. Químicamente es bastante inerte, resiste el ataque con el aire, el agua, ácidos y reactivos ordinarios, y sólo se disuelve lentamente con el agua regia. Es un metal muy pesado con una densidad de 21.45 g/cm3 y símbolo químico Pt.
El francés Lavoisier escribió en 1786 una carta sobre sus experimentos de 1782 para fundir el platino proveniente de "los dominios españoles en América", y sólo hasta 1800 el químico británico W.H. Wollaston pudo purificarlo hasta hacerlo maleable.
Qué son la minería, la metalurgia y el beneficio
En la naturaleza son muy escasos los metales puros, casi todos se encuentran asociados químicamente con otros elementos formando compuestos conocidos como minerales. El mineral o conglomerado de minerales útil para la obtención de metales se conoce con el nombre de mena y se llama yacimientos a los sitios donde se encuentran acumuladas las menas.
En las menas los minerales se encuentran combinados con elementos como azufre, cloro u oxígeno para formar sulfuros, silicatos, cloruros, carbonatos u óxidos. Los carbonatos de cobre, por ejemplo, son verdes vistosos (malaquita) o azules (azurita) o de color rojo fuerte (cuprita). Al estar expuestos en la superficie son fácilmente visibles.
A pesar de su escasez, ocasionalmente se encuentran concentraciones de metales nativos en la corteza terrestre en áreas relativamente pequeñas; este es el caso del oro, la plata, el cobre y metales del grupo del platino. Los yacimientos de cobre nativo más grandes, famosos y con evidencias de producción de larga data son los de la Isla Royale en los Grandes Lagos de Norteamérica.
Los metales pueden encontrarse concentrados (yacimientos masivos), en vetas o en yacimientos sueltos (gravas en el lecho de los ríos) también conocidos como placeres.
La minería consiste en la extracción selectiva de minerales y otros materiales a partir de la corteza terrestre, con frecuencia en grandes cantidades para recuperar sólo pequeños volúmenes del producto deseado. En la actualidad se reconocen cuatro tipos básicos de métodos de minería:
1. Minas de superficie o explotaciones a cielo abierto. Constituyen la inmensa mayoría de las minas de todo el mundo 2. Minas subterráneas a las que se accede a través de galerías o túneles 3. Pozos de perforación 4. Minería submarina o dragado
Dentro de la minería de superficie algunos técnicos ubican las minas de placer. Los placeres son depósitos de minerales mezclados con arena o grava. Suelen estar situadas en los lechos de los ríos o en sus proximidades, en terrenos aluviales, de ahí que también se le conozca como minería de aluvión. La naturaleza de los procesos de concentración que dan lugar a los placeres, permiten que en estos depósitos se obtengan materiales densos y ya liberados de la roca circundante. Esto permite un proceso de extracción y limpieza relativamente sencillo que se limita al movimiento de tierras y al empleo de sistemas sencillos de recuperación física del metal. Los ríos y arroyos pueden recuperar sus niveles de agregados siempre y cuando las condiciones geológicas y medioambientales no cambien río arriba.
Los placeres se explotan de forma industrial mediante el dragado con máquinas mecánicas pero suelen ser explotados artesanalmente con el uso de una batea de madera para recoger la arena y la grava y limpiarla. Al hacer girar agua, arena y pequeños granos de oro, éstos por ser más pesados tienden a quedar en el fondo de la batea y son detectados por el minero.
La minería subterránea correspondiente a los metales es minería de roca dura. Es necesaria cuando la mena se encuentra a gran profundidad y para llevarla a la superficie se requieren pozos y túneles.
Se presume que en un principio no se utilizaron túneles o socavones para la minería, si no que se exploraba la montaña buscando la zona en la que la veta llegaba a la superficie. En algunos casos se encuentran los metales nativos en la superficie. Se piensa que la metalurgia se inició con el trabajo del cobre, precisamente debido a los llamativos colores de los minerales de las menas que lo contienen, los cuales pudieron haber inducido al hombre a recogerlos y a tratar de elaborar con ellos objetos semejantes a los que hacían con otras piedras.
La metalurgia y el beneficio de los metales
La metalurgia es el arte de extraer metales de sus menas, refinarlos y prepararlos para su uso. El proceso consiste en modificar la naturaleza química de los minerales para separar el metal de sus compuestos sulfúricos, óxidos, silicatos o carbonatos. Estos métodos dependen mucho del tipo de mena y de su composición química; en algunos casos este es un proceso mecánico, por ejemplo, cuando el oro se recupera de su núcleo pulverizándolo y después pasándolo por lavado en agua.
Los metales obtenidos por los diferentes métodos de metalurgia extractiva por lo general contienen impurezas tales como otros metales, elementos no metálicos, pequeños restos de escoria y gases disueltos. La remoción de tales impurezas es el refinamiento o beneficio de los metales y es necesario para permitir que el metal sea trabajado posteriormente. Muchas de las propiedades de los metales importantes para el orfebre (maleabilidad, ductilidad, brillo, color, dureza, etc.) se ven afectadas o favorecidas por las impurezas. El oro recuperado en los procesos extractivos generalmente contiene cantidades significativas de cobre, plata y trazas de metales del grupo del platino; para la refinación de cierto punto en adelante, se necesitan procesos más complicados como la electrólisis.
El separar y extraer los metales de las concentraciones de minerales es un trabajo delicado y que requiere mucha destreza. Se hace en la actualidad en casas de fundición o refinerías y los métodos empleados incluyen la pirometalurgia, electrometalurgia e hidrometalurgia. En épocas prehispánicas se utilizaron métodos que incluían la acción del fuego o pirometalurgia. Lograr obtener cobre fue un gran paso en el origen de la metalurgia, debido al proceso dispendioso que significa la reducción del cobre a partir de los minerales. Para el oro el proceso es más fácil.
Los carbonatos suelen estar en la parte superior de los afloramientos minerales y su reducción es relativamente sencilla, por lo que se piensa que éstos debieron ser los primeros minerales que el hombre aprendió a reducir. El proceso consiste en moler los carbonatos, mezclarlos con carbón de leña y dispuestos en el interior de un crisol o de una vasija de cerámica refractaria introducirlos en un horno u hoguera para fundirlos; el carbón junto con el calor producen la descomposición de gases de carbono (monóxido y dióxido de carbono) y el cobre queda libre (como metal líquido puro) y se deposita en el fondo del crisol formando un botón. Este es el proceso conocido como reducción. Los desechos líquidos adicionales se conocen como escoria.
Las menas más profundas formadas por sulfuros requieren procesos más dispendiosos. Los sulfuros deben ser sometidos a tostación o calentamiento al aire. Por acción del calor el azufre de los sulfuros se desprende y pasa a formar óxidos de azufre (anhídrico, sulfuroso y sulfúrico), mientras que el cobre se oxida y forma óxidos de cobre como la cuprita y tenorita. La tostación debe seguir hasta que se desprendan todos los gases y entonces los óxidos resultantes se pueden reducir al mezclarlos con carbón y someterlos a calor, en un proceso igual al de la reducción de carbonatos.
Las temperaturas necesarias para realizar a cabalidad estos procesos de reducción o fundición dependen de los puntos de fusión de cada metal. El oro funde a 1.063°C; el cobre, a 1.083°C, la plata a 963°C y el platino a 1.773°C.
Para fundir y separar los metales de la ganga o materiales adicionales considerados como inservibles, es necesario lograr las temperaturas suficientes para derretir los metales deseados. En la actualidad, las menas se calientan (calcinan) en hornos en presencia de carbón (coque) y es usual el uso de fundentes como la piedra caliza para facilitar la fundición.
Una historia del trabajo de los metales
La vida moderna es posible gracias a que conocemos los metales y sabemos cómo usarlos. Estos soportan nuestros edificios y puentes, nos permiten volar, navegar y desplazarnos, sustentan la producción industrial y el comercio. Con los metales medimos el tiempo, hacemos monumentos, rendimos culto, nos adornamos, producimos arte y hacemos la guerra. Pero esto no ha sido siempre igual.
[1] Historia de los metales un video de museodeloro en Vimeo.
Antiguamente no se conocían los metales. Cuando se descubrieron y se aprendió a trabajarlos cambió la vida de los pueblos. La historia de los metales se inició hace cerca de nueve mil años en el Próximo Oriente. El primer metal utilizado fue el cobre; en Palestina y Anatolia los antiguos pobladores martillaron trozos de cobre nativo para formar herramientas. En los siguientes siglos se aprendió a extraer cobre de los minerales y mezclarlo con estaño para formar bronce.
El bronce le permitió a los imperios de la antigüedad producir armas para los ejércitos de conquista. La agricultura y la artesanía tuvieron herramientas fuertes y la producción creció. Desde entonces los metales sirvieron para muchos fines. El oro y la plata adornaron a los grandes personajes y los acompañaron en sus sepulcros. El culto religioso se sirvió de ellos para elaborar ornamentos y símbolos.
Nuevos procesos técnicos hicieron posible utilizar otros metales: herramientas y armas más fuertes, edificios reforzados con ganchos y puertas con cerraduras y herrajes. El hierro le dio a las naciones que lo producían una gran ventaja; en estos reinos los gobernantes demandaron más y mejores adornos. Crecieron así, lado a lado, la metalurgia del bronce y el hierro y la orfebrería del oro y la plata.
Para el 1000 antes de Cristo casi todos los pueblos del Viejo Mundo tenían metales; desde el Mediterráneo, pasando por Persia e India, se hicieron en bronce y oro armas, instrumentos y adornos variados. Desde China la metalurgia se extendió a Japón, en donde los aceros armaron a los samuráis, y también al sureste asiático cuyos templos se coronaron con cúpulas doradas.
Para la época en que cayó el Imperio Romano los implementos de metal eran parte de la vida diaria. Ya no se podía entender el comercio sin la moneda ni las actividades cotidianas sin herramientas metálicas. Las religiones del mundo antiguo en Asia, África y Europa, recurrieron al oro y la plata para forjar los objetos sagrados. En el convulsionado mundo medieval chocaron en la guerra los metales de Occidente y los de Oriente.
Desde 1300 los estados del occidente de África, al sur del Sahara, usaron el bronce para decorar las ciudadelas reales. Para surtir de materias primas a los herreros y distribuir sus productos se organizaron caravanas que cruzaban el desierto. Los orfebres africanos se convirtieron en maestros de la fundición; los adornos y delicadas miniaturas comunican una profunda simbología.
Los antiguos suramericanos empezaron a trabajar el cobre y el oro alrededor de 1500 antes de Cristo. Unos mil años más tarde varias culturas andinas adornaban a sus líderes con suntuosos atuendos. El oro y la plata se reservaron para los gobernantes y la religión; los objetos rituales y simbólicos comunicaban una visión del mundo que compartía toda la sociedad.
En el año 500 de nuestra era la metalurgia ya era una actividad corriente desde México central hasta el norte de Chile y Argentina. En cada región surgieron estilos propios: en México, figuras en lámina; en Centroamérica, pequeños adornos de oro; en Colombia y Ecuador, adornos de tumbaga dorada; en Perú, coloridos atuendos de cobre dorado y plateado; en los Andes del sur, placas de bronce.
La metalurgia en la Colombia prehispánica fue, ante todo, orfebrería. En dos mil años surgieron muchos estilos diferentes y se fabricaron miles de piezas para el ritual y la ofrenda. Los indígenas manejaron con maestría el oro, el cobre, la tumbaga y el platino. La conquista europea, en 1500, truncó este desarrollo y causó la desaparición de la producción orfebre.
En los últimos 300 años la producción de metales ha tenido un gran avance. La gran industria usa millones de toneladas de metales cada año; también las sociedades no industriales consumen cada vez más metales para los más variados propósitos. La historia de la humanidad en los últimos nueve mil años es la historia de los metales: con ellos hemos construido el mundo en que vivimos.
Mineros y orfebres: un relato desde sus instrumentos de trabajo
En épocas prehispánicas los mineros se procuraban el oro, el cobre y el platino lavando las arenas auríferas de los ríos que bajaban de las cordilleras, en especial de la Central y la Occidental. También explotaron vetas en las montañas.
Los españoles que los vieron trabajar tras la Conquista contaron en sus escritos y crónicas que los indígenas eran expertos en estos trabajos; que usaban bateas de madera y cerámica para lavar con agua la arena de los ríos, que construían acequias, canales y acueductos para desviar las aguas y llevarlas hasta los sitios de extracción; que quemaban y rozaban potreros para hacer aflorar los depósitos auríferos y recoger el metal en las raíces de las plantas carbonizadas; que atravesaban redes y mallas en los ríos correntosos para atrapar las pepas grandes del metal; que abrían socavones de hasta seis metros de profundidad y que para romper las peñas en busca del oro las calentaban con grandes hogueras y las bañaban luego con agua fría.
Los instrumentos mencionados para la perforación eran la coa o macana con la punta endurecida al fuego y rudimentarias pero efectivas herramientas talladas en piedras duras. En canastos de fibras vegetales se transportaba la tierra y el material aurífero.
Hachas, martillos o barretones de piedra sin duda pudieron servir para abrir socavones y canales y seguir las vetas de los metales. Hoy los arqueólogos podemos identificar certeros vestigios de las actividades mineras cuando dentro de las tumbas, el difunto, presumiblemente un minero, fue enterrado junto con pepitas o chicharrones de oro o con oro en finas lentejuelas, producto del bateaje.
El oro obtenido en forma de chicharrón o pepita era triturado en morteros de piedra con la ayuda del agua de arroyos cercanos. Los minerales de cobre tenían que ser fundidos junto con otras sustancias para separar el cobre metálico de otras impurezas. Esto se realizaba en hornos construidos en las laderas de las montañas para aprovechar las corrientes de aire, de manera que éstas ayudaran a mantener el fuego. En hornos cavados en la tierra el fuego era mantenido por la acción de varios indígenas que se turnaban en la tarea de soplar a través de cañas verdes, delgadas y largas con los extremos protegidos del calor por tubos cerámicos o toberas. Las toberas presentan diferencias de color y de diámetros en sus extremos. Algunos son cilíndricos con un borde en forma de cono y otros tienen forma de conos alargados unidos por su base. Dos de la colección del Museo del Oro están decoradas con rostros humanos.
No sólo se fundió en hornos cavados en la tierra, también en hornillas o braseros portátiles que estaban en uso en la época de la Conquista. Hechas en cerámica, están formadas por una base dentro de la cual se soplaba por un tubo al que se ensamblaba una caña, y tienen varios pequeños orificios por donde el aire pasaba de la parte inferior a la superior a través de las brasas de carbón vegetal. El aire a presión avivaba así el fuego para obtener las temperaturas superiores a los 1.063° necesarias para la fundición.
Los minerales se fundían dentro de crisoles de cerámica refractaria, al fondo de los cuales quedaban pequeños tejuelos o lingotes redondos y planos del metal listo para ser trabajado. Fundiendo en un crisol oro argentífero y cobre se creaba la aleación que conocemos como tumbaga.
Los orfebres de la Cordillera Oriental, del Altiplano Nariñense y de la Sierra Nevada de Santa Marta usaron piedras duras, resistentes y muy lustrosas como utensilios de trabajo. En piedras negras y verdes con diferentes composiciones de minerales de hierro, basaltos u obsidianas, tallaron yunques, punzones, cinceles, repujadores y pulidores. En algunos de estos artefactos se ven ralladuras doradas que delatan su uso en el trabajo de los metales. Martillos los hubo de diferentes tipos de piedra, tamaños y formas, según el tipo de lámina que se necesitara hacer, el avance del trabajo e incluso la aleación del metal trabajado, puesto que el oro se podía martillar mucho más fácilmente que la tumbaga, que es relativamente dura.
Cinceles, punzones y repujadores también se hicieron en metal para cortar y repujar las láminas metálicas haciendo presión sobre ellas. Era usual que fueran de tumbaga o incluso de cobre endurecidos a golpes de martillo hasta quedar más duros que el material sobre el que se trabajaba. En muchas ocasiones un solo instrumento tenía doble función o se usaba engastado en mangos de madera.
Además de los martillados y repujados, gran cantidad de adornos y recipientes fueron hechos por la técnica de la fundición a la cera perdida. El orfebre limpiaba, colaba y amasaba la cera obtenida de los panales de abejas sin aguijón para hacer modelos con la forma que deseaba darle a las figuras de metal. Sobre mesas de piedra estiraba la cera con rodillos de piedra para volverla láminas o hilos que cortaba con cinceles, cuchillos y espátulas de piedra o metal. Estos utensilios le servían también para alisar y pulir la figura delicadamente armada en cera. Para crear un molde el orfebre cubrió luego cada uno de sus modelos de cera con arcilla, primero muy líquida y mezclada con carbón molido, luego más consistente. Una vez seca la arcilla, calentó el molde: la cera se derritió y salió por unos canales dejados para ese efecto, y su lugar —y su forma— fueron ocupados por el metal fundido que el orfebre vertía desde el crisol. Alguna forma de pinza debieron usar los metalurgos para tomar el crisol de entre las brasas ardientes y llevarlo hasta el molde con el metal fundido.
Hay un largo camino entre la veta o las arenas auríferas y el objeto ya pulido, retocado y bruñido que el orfebre podía mostrar con orgullo a su cacique y su comunidad, o depositar, como ofrenda, en lo profundo de un bosque o en las aguas de una laguna. Ese camino está registrado en las mútiples herramientas que preserva la colección del Museo del Oro.
Martillado
Una técnica de la metalurgia prehispánica colombiana
Martillado de museodeloro en Vimeo.
Fundición a la cera perdida
Una técnica de la metalurgia prehispánica colombiana
Fundición a la cera perdida de museodeloro en Vimeo.
De la manera de labrar los plateros
Por fray Bernardino de Sahagún
Nota. El siguiente es un aparte de los documentos en Náhuatl allegados por fray Bernardino de Sahagún para su Historia general de las cosas de Nueva España, donde los propios indígenas mexicanos describen minuciosamente el proceso de fundición a la cera perdida. Los oficiales que labraban oro y plata se dividían en dos o tres especialidades: unos eran los martilladores, amajadores o batihojas que «labran el oro de martillo» y «no tienen más oficio que batir el metal fino, adelgazarlo, con piedras extenderlo donde sea necesario y laminarlo»; «otros se llaman ajustadores» que Sahagún considera artistas porque al parecer repujaban, ensamblaban y engastaban; «otros se llaman tlatlalianime que quiere decir que asientan el oro o alguna cosa en el oro o en la plata y estos son verdaderos oficiales que por otro nombre se llaman tolteca y son «los fundidores» del metal fino». Los dibujos originales y el dictado hechos por los principales indígenas datan de 1548 a 1561; la obra española de Sahagún, de 1582, no contiene este texto que fue traducido del Náhuatl por el padre Ángel María Garibay para la edición de 1956 por Editorial Porrúa (tomo 3, págs. 67-72). Los dibujos que publicamos provienen de la copia del Códice Florentino, muy posterior.
Aquí se declara en qué manera hacían algo los fundidores de metales preciosos. Con carbón, con cera diseñaban, dibujaban algo: con lo que fundían metal precioso, sea amarillo, sea blanco.
Con esto daban principio a su arte. Primeramente el que presidía les repartía carbón. Primero lo muelen bien, lo hacen polvo, se lo reducen a menudo polvo.
Y ya que lo han molido, luego lo juntan, lo mezclan con un poco de lodo de ollero, el que es pegajoso, con el que hacen ollas. Con esto desaparece, desbasta, hace pegajoso al carbón, con esto se endurece, se adelgaza
Y cuando lo han acabado, de igual manera hacen laminillas, las tienden al sol, y otras laminillas hacen de semejante manera que ponen al sol.
En dos días se secan, se resecan, se enjutan, se endurecen. Cuando se ha secado bien, cuando se ha endurecido, luego se graba, se moldea el carbón con una navajilla de metal.
Si se comienza la figura de un ser vivo, de un animal, se graba, no más se sigue la semejanza, se imita lo vivo, para que en ello salga lo que se quiere hacer.
Supóngase que es un huasteco, un vecino: tiene su nariguera, su perforación de la nariz, su flecha en la cara, su cuerpo pintado con navajillas de obsidiana (tatuado): enteramente así se dispone el carbón al irse raspando, al irlo labrando cuidadosamente.
Se toma de cualquier cosa que se trata de ejecutar: como es su natural y su apariencia se dispondrá.
Sea (verbigracia) una tortuga: exactamente así se dispone el carbón: su caparazón con que se irá moviendo, su cabeza que sale de dentro de él, que se mueve, su pescuezo y sus manos, como que las está extendiendo.
O sea un pájaro el que va a salir del oro: enteramente así se tallará, así se raspará el carbón: de modo que adquiera sus plumas, sus alas, su cola, sus patas.
O sea un pescado que se va a hacer: enteramente así se raspa el carbón: adquiere sus escamas, sus aletas, así se acaban, y así está parada su cola bifurcada.
O bien, se ha de hacer una langosta acuática, o una lagartija; se le ponen sus manos, sus patas (en esta forma) se labra el carbón. Cualquier cosa que se ensaye hacer, un animalillo o un collar de oro que se ha de producir, con cuentas como semillas, con campanitas al borde, cosa de artificio, engalanada de flores.
Cuando se acaba de grabar el carbón, cuando se ha esculpido, luego se hierve la cera, mézclase con incienso blanco de la tierra (copal), con el cual se endurece bien. Enseguida se purifica, se tamiza, para que con esto caiga su suciedad, su tierra, su lodo de la cera.
Y cuando ya está lista la cera, luego en una laja se adelgaza, se hace lámina con un rodillo de madera. Esa piedra laja es muy lisa, sumamente lisa, en la cual se adelgaza y lamina (la cera).
Y cuando se ha adelgazado bien, como una telaraña, que ya no tiene grumos ni bolillas en parte alguna, luego se pone en el carbón, se extiende sobre la superficie; pero no se pone sin gran cuidado, sino con tiento, poco a poquito se va cortando, se va despedazando, de modo que entre en los huecos; se pone en las estrías, en las cavidades y entradas, se embute donde se ha labrado el carbón; con un palito se va pegando.
Y cuando se ha acabado de poner por todas partes la cera, luego se tiende polvo de carbón en agua sobre la superficie de la cera. Se muele bien, se pulveriza el carbón; un poco grueso se tiende en la superficie de la cera.
Y una vez que se ha hecho esto, otra vez se le pone una capa con que se reviste por completo y se cubre enteramente, con lo cual ya es el momento de dejar la obra con que se ha de fundir el oro.
Esta capa es puramente carbón, mezclada con barro pegajoso, no muy molido, sino basto.
Cuando se ha cubierto y revestido lo que se moldea, por dos días aún se seca, y luego se le pone el tubo para el oro, también hecho de cera; ése es el tubo que se le hace al oro. Por allí ha de entrar cuando es derretido y otra vez con él se conecta. Se dispone el crisol, también es de carbón, de hechura ahuecada. Luego así se toma el carbón; allí es cuando se funde y liquida el oro, con lo cual luego entra el tubo de comunicación, con esto se entuba por allí y corre. Se pone en el suelo.
Cuando se ha fundido el artefacto, el collar que se intentó, o cualquiera de las cosas mencionadas, se pule con un pedrusco, y cuando ya se ha pulido, es cuando se le da un baño de alumbre. Otra vez entra al fuego, con el cual se calienta, y cuando ha sido sacado, una vez más se baña, se restriega con el que se llama «remedio del oro» . Esto es solamente como una tierra amarilla: se mezcla con un poco de sal, y con ésta se perfecciona, se pone muy amarillo el oro.
Y luego se desnuda, se frota, con lo cual se hermosea mucho, y viene a brillar mucho, a resplandecer, a echar fulgores de sí.
Dicen que antaño solamente andaba el oro y de él disfrutaban. Lo fundían los aurífices y hacían collares de él.
Por su parte los batihojas lo laminaban y adelgazaban: se empleaba para las insignias militares. No había aún plata: rara vez se hallaba; aquí o allá se dejaba ver, con lo cual era muy apreciada.
Pero ahora todo es plata. Quieren el oro y es muy tenido en precio.
Los plateros, lo mismo los de fundición que los batihojas, ahora al hacer algo de plata, requieren un metal rojo, aunque solamente para que sirva de base a la plata, para colocar plata en él; con ello chapean y emplastan.
Que si sola la plata se funde y se usa, no más se hace pedazos el artefacto al lavarlo, no es consistente en todas sus partes, ni se compagina en donde están colocadas las aplicaciones.
Antaño los batihojas solamente se dedicaban a batir el metal fino; lo hacían maleable, lo adelgazaban muy bien y lo pintaban con rayas negras.
En primer lugar, les escribían (el objeto) los trabajadores de pluma, luego ellos lo dibujaban con un pedernal; iban siguiendo el contorno de la línea negra, de modo que quedara escrito y dibujado con el pedernal; le hacen realces, le van haciendo lentamente los realces, para que quede tal como es el modelo.
Ahora, en donde quiera que se necesita su obra, ya sea de pintura de plumas, ya sea de artefacto de plumas, se requiere que se les asocien y se les enseñe a los aurífices los artistas de la pluma. De esta manera labran todo lo que quieren unidos a los de arte plumaria.
Ahora, al hacer alguna cosa los aurífices, necesitan de arena, arena fina. Después que la han conseguido, la muelen, la remuelen, y también la mezclan con pegamento.
Luego la extienden en la misma forma que extienden el lodo, para que en ella salga, en ella se imprima cualquier cosa que han de hacer.
En dos días se seca; cuando se ha secado bien, con un fragmento de tiesto se raya, se raspa, se restriega; con ello queda lisa la superficie. Enseguida se traza el grabado con un punzón de metal, como en otro lugar está declarado.
Como en dos o tres días queda acabado, compuesto y perfeccionado el artefacto. Cuando se ha terminado, se le pone encima polvo de carbón en agua,y con pegamento se fija el carbón en la superficie.
Tras eso, luego se hierve la cera, se le mezcla incienso blanco de la tierra (copal), como se declaró.
Cuando se ha enfriado y está clarificada, luego se adelgaza en una laja con un rodillo de palo, que se hace rodar sobre ella. Enseguida se le aplica encima una capa de lodo, con la cual se moldeará el oro (al fundirse), en figura de cualquier objeto que se ha de hacerse, sea un jarro, o un sahumerio, que llaman «perfumador».
Al pintar y disponer una buena pintura principalmente es muy apta la cera; esto principalmente lo hace el pintor artístico, con esto se hace obra de arte, pues principalmente primero en alguna parte se hace el molde de cera.
Cuando se ha preparado todo, en ella se aprieta el molde, pues en él se halla la impresión de cualquier artificio vgr. un ala, una cola de pájaro, o una flor, o una rama de planta, o cualquier cosa de hermoso aspecto.
Se va apretando, se va pegando con un palito que llaman «punzón de palo».Como en dos días se ajusta, se compone. Cuando se ha ajustado, por todas partes se le pega cera, para extender luego en la superficie polvo de carbón con agua.
Cuando se ha secado, es precisamente cuando se le ponen las tapas, de puro carbón basto, con lo cual se reviste totalmente el molde. Como en dos días se seca.
Luego se le pone en la cera el llamado tubo de contacto, es cilíndrico, primeramente se redondea: éste es el conducto por donde ha de entrar el oro. Puesto el tubo, luego se van poniendo los crisoles en que se ha de derretir el oro.
Cuando todo se ha dejado listo, como va dicho, luego se pone en el fuego, se calienta totalmente: allí sale, arde la cera que se halla dentro, la que se había puesto.
Cuando ya se fue la cera, cuando ardió, luego se enfría: es entonces cuando se coloca sobre la arena burda.
Es cuando, por fin, se funde, entra al crisol, se pone en el carbón, y el oro que allí entra por otro lado en un cucharón se derrite. Allí acaba todo esto, con esto queda hecha la obra.
Cuando ha nacido, se ha fundido y ha sido hecho el artefacto, luego va a un baño de alumbre, en un cazo de cobre, en el cual hierve a borbollones.
Y si en alguna parte está rota la obra, o se dañó, es el momento de remediarla. Se pega con soldadura y luego se raspa con una azuelilla y con ella se pule.
Otra vez se mete a donde está el alumbre, se le aplica alumbre, y después se limpia, se pulimenta, queda bien limpia.
Fundiciones especiales
La técnica básica de la fundición a la cera perdida fue desarrollada para crear técnicas especiales, variantes más complejas que permitían manejar el color de los objetos, hacer poporos y otros recipientes vacíos en su interior, hacer en serie impresiones de motivos decorativos.
Fundiciones múltiples
Los orfebres prehispánicos lograron objetos articulados o multicolores fundiendo {a la cera perdida} en varias etapas, con aleaciones cuyos puntos de fusión eran cada vez más bajos.Mediante fundiciones sucesivas a la cera perdida se hicieron, por ejemplo, los alfileres bimetálicos, únicos en América, que proceden del Valle del Cauca. Un ave que balancea su cabeza y cola está formada por partes independientes hechas con distintas aleaciones. La cabeza y la cola fueron hechas en una aleación alta en oro, al igual que el eje sobre el cual se mueven; el cuerpo fue fundido luego en una tumbaga más cobriza, que funde a menor temperatura. La segunda fundición. por lo tanto, no alcanza temperaturas que dañen los objetos hechos primero.
Las etapas de este proceso de manufactura ideado por los antiguos orfebres son las siguientes, ilustradas con la elaboración de un alfiler o palillo para cal cuyo remate representa un personaje de piel cobriza ataviado con adornos de oro.
1. Los adornos se martillaban o fundían en oro y se daba forma a un modelo en cera de abejas purificada. 2. Los adornos se colocaban sobre el modelo de cera, en la posición que debían tener en la pieza final. 3. El modelo era recubierto con un molde de arcilla. 4. Calentando el molde salía la cera y dejaba la forma de la figura impresa en el molde de arcilla, con las piezas de oro en su posición. 5. Se vaciaba entonces la aleación de oro-cobre, que por tener una temperatura de fusión más baja que el oro no derretía los minúsculos adornos. 6. Para sacar el objeto una vez enfriado era necesario fracturar el molde para sacar la pieza y pulirla.
Fundición con núcleo
Para crear objetos tridimensionales o huecos, los orfebres modelaban primero las figuras o recipientes en una mezcla de arcilla y carbón. Revestían este núcleo con la cera que habría de transformarse en metal y aplicaban la decoración. Cubrían luego con arcilla para formar el molde, pero antes de extraer la cera para verter el metal debían clavar astillas o palitos, llamados tabiques, para que al derretirse y salir la cera el núcleo interno y el molde externo conservaran su posición, separados por el espacio donde debía entrar el metal fundido.
Los grandes poporos o recipientes para cal procedentes del período Quimbaya del valle medio del río Cauca fueron hechos con este método. Después de extraer el carbón del interior, los orificios dejados por los tabiques en las paredes del objeto se taparon con remaches del mismo metal que pueden verse en las gammagrafías, como pequeñas manchas oscuras.
En la Cordillera Oriental los orfebres integraron los orificios de los tabiques al diseño de la pieza —figuras o adornos— y no fue necesario utilizar remaches.
Cuando no se trataba de reciíentes, este método representa un gran ventaja para los arqueólogos: el carbón vegetal de los núcleos puede analizarse mediante el método del radiocarbono para conocer las fechas aproximadas en las que fueron manufacturados los objetos.
La fundición a la cera perdida es compleja en todas sus variantes. Durante el proceso de fundición fueron frecuentes los accidentes: falta de materia prima, temperaturas muy bajas o muy altas, entre otros. Limaduras, desechos y algunos objetos defectuosos se fundían para reutilizar el metal.
Matrices de piedra
Los orfebres de la Cordillera Oriental tallaron sellos o matrices en piedras blandas para estampar con ellos delgadas láminas de cera que eran transformadas luego en metal por el proceso de la cera perdida.
Los muiscas usaron "collares" que en realidad no se ponían alrededor del cuello y sobre el pecho sino dos a la vez, terciados sobre el pecho y la espalda: uno alrededor del cuello y del hombro izquierdo, pasando bajo el brazo; otro de la misma forma al lado derecho. Las cuentas de esos collares son laminillas rectangulares de forma básicamente rectangular y presentan el mismo motivo repetido. No fueron hechas por laminado y luego repujado sobre un modelo de madera o piedra, como las hay en la región Calima: son fundidas a la cera perdida.
De la observación de esas cuentas puede deducirse el procedimiento siguiente:
1. Se purificaba y laminaba la cera de abejas, hasta producir tiras semejantes a la cinta pegante de un grosor ligeramente menor a un milímetro. 2. Sobre una superficie de arcilla mezclada con carbón molido se estampaba una de las figuras talladas en el sello, cuya forma entonces quedaba hundida en la arcilla. Este será luego el frente de la cuenta. 3. Dejando secar probablemente la arcilla para que adquiriera consistencia, se colocaba sobre ella la lámina de cera y se estampaba de nuevo. Alguans matrices parecen incluso tener unas guías para facilitar el case de las dos impresiones. 4. La cera, ya con sus dos caras estampadas, se recortaba con una cuchilla para dejar la forma rectangular y eliminar los excedentes. El corte no se pulía y es visible en las cuentas. 5. Se colocaban tiras de cera para ser los conductos por donde saldría la cera y entraría el metal, y se recubría con más arcilla hasta formar un molde cerrado con muchas cuentas adentro. 6. Como en el procedimiento normal de la cera perdida, el molde se calentaba para sacar la cera y vertir el metal. Luego se rompía para sacar las cuentas.
El poporo Quimbaya
El muy conocido poporo quimbaya que motivó la creación de la colección arqueológica del Banco de la República fue elaborado a la vez con núcleo y en dos fundiciones sucesivas. Una gammagrafía muestra los orificios remachados de los tabiques usados para soportar el núcleo, pero en ella se ve además una parte negra más densa en la base, que en la superficie del objeto muestra al análisis visual un cambio de color.
El orfebre talló en arcilla y carbón la forma del interior y la cubrió con cera. Le agregó una decoración en la cintura, pero sobre todo una delicada base cónica hecha con hilos de cera. Fundió esta parte inferior inicialmente, como para garantizar que la base quedara muy bien, y luego el resto del recipiente.
Finalmente sacó el carbón del interior, por la boca, y pulió y bruñó la superficie hasta hacerla brillar con el fulgor del sol.
Dorado por oxidación
Una técnica de la metalurgia prehispánica colombiana
Dorado por oxidación de museodeloro en Vimeo.
[5]Lea un fragmento de la crónica de Gonzalo Fernández de Oviedo (Libro IV, capítulo VIII) sobre el dorado con hierbas.
Del Boletín Museo del Oro: Un caso de alteración aurífera colonial en el Bajo Magdalena
Diagrama ternario
¿Cómo leer y para qué sirve un [6]diagrama ternario? El triángulo ampliamente usado en arqueometalurgia para graficar la composición de un objeto de tumbaga (aleación de oro argentífero y cobre), explicado por [7]Marcos Martinón-Torres, arqueólogo y co-guionista de la exposición Historias de ofrendas muiscas.
No se pierda la exposición del Museo del Oro del Banco de la República en PDF:
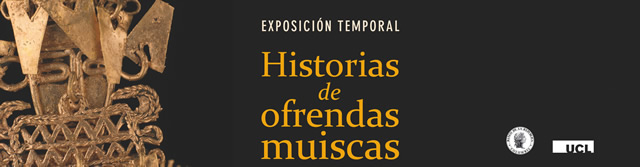